Designing and Developing the Structural Coupling Test Facility for LCA AF Mk2: A Comprehensive Overview
NEWS
3/24/20253 min read
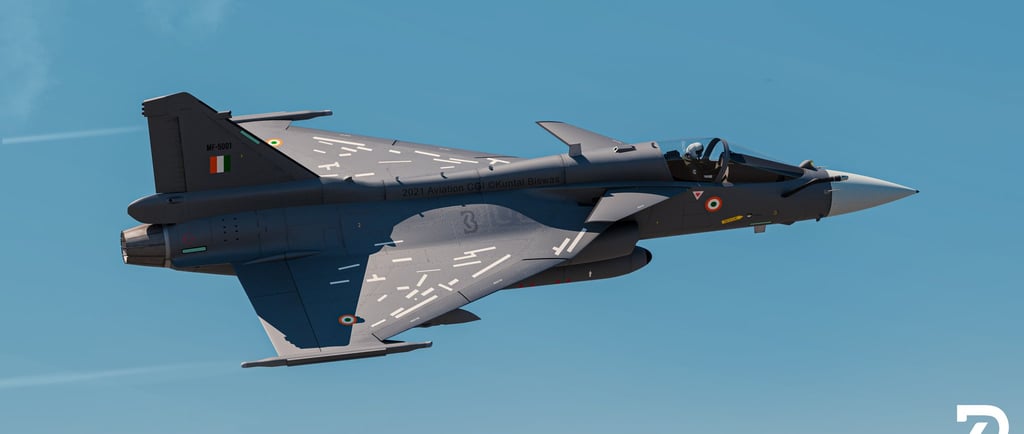
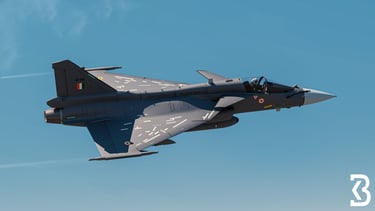
The Light Combat Aircraft (LCA) AF Mk2, an advanced fighter jet under development by the Aeronautical Development Agency (ADA) in India, represents a significant leap in indigenous aerospace technology. A critical component of its development is the Structural Coupling Test Facility (SCTF), which ensures the aircraft’s flight control system (FCS) integrates seamlessly with its structural framework. This article delves into the intricacies of designing, developing, integrating, validating, testing, and commissioning the SCTF, as outlined in detailed procurement documents released by ADA and hosted on the Government e-Marketplace (GeM) portal.
Purpose and Importance of the SCTF
The SCTF is pivotal in the LCA AF Mk2’s development phase, serving as the first integration test conducted after the aircraft’s structural assembly reaches flight standards. This test is essential not only during initial assembly but also whenever significant modifications alter the airframe’s structural characteristics. The primary objectives of the SCTF are twofold: to quantify structure-control coupling frequency regions and levels for designing FCS notch filters, and to demonstrate the adequacy of structural stability margins. These outcomes ensure the aircraft’s safety and performance under various flight conditions.
Technical Specifications and Components
The SCTF is a sophisticated system comprising hardware and software tailored to the LCA AF Mk2’s requirements. Key deliverables include:
Industrial PCs: Four units with high-end specifications (i9 processor, 64 GB RAM, 1 TB SSD, 2 TB HDD) to handle real-time data processing and analysis.
Break-Out Boxes (BOBs): Active and passive BOBs to manage signal routing between the aircraft’s Digital Flight Control Computer (DFCC), auxiliary computer, and primary actuators/motion sensors.
Frequency Response Analyser (FRA): A core component for analyzing transfer functions, with a spare card to ensure redundancy.
Signal Generators and Data Acquisition Systems: For injecting test signals and capturing responses from actuators and sensors.
Cable Harnesses and Connectors: Custom-designed looms meeting aircraft-grade standards (e.g., D38999 connectors) for reliable interfacing with the aircraft’s Ground Maintenance Panel (GMP).
Ancillary Equipment: Oscilloscopes, digital multimeters, frequency counters, and a printer for on-site diagnostics and documentation.
The system supports a variety of analog and discrete signals, such as actuator positions (±5 VDC to ±10 VDC) and health status indicators (Open/GND, ±15 V), with stringent accuracy requirements (0.01% of full scale). The graphical user interface (GUI), developed using licensed LabVIEW software, provides user-friendly control over test configurations, data acquisition, and real-time analysis.
Development Process and Vendor Responsibilities
The procurement documents outline a rigorous process for vendors, emphasizing a systems engineering approach:
Design and Planning: Vendors must study the existing SCTF architecture, finalize hardware and software requirements in consultation with ADA, and submit detailed development plans, block diagrams, and compliance matrices.
Hardware Development: This includes procuring OEM components, designing PCBs, fabricating test jigs, and ensuring compatibility with aircraft industry standards for power, grounding, and environmental conditions (0°C to 50°C, 20% to 90% RH).
Software Development: Vendors are tasked with creating software modules (including source code) for signal generation, data acquisition, and frequency response analysis, adhering to a Software Development Life Cycle Process.
Integration and Testing: The SCTF undergoes standalone and integrated Acceptance Test Procedures (ATPs) at the vendor’s site, the IFCS test rig, and the final SCTF location at Hindustan Aeronautics Limited (HAL). Certification from agencies like CEMILAC and RCMA is mandatory.
Documentation: Comprehensive deliverables include hardware/software requirement specifications, design documents, test reports, and user manuals, all approved by certification bodies.
Vendors must demonstrate significant experience—minimum 10 years in automated test equipment (ATE) development for defense and aerospace, with expertise in PXI/PXIe systems and LabVIEW-RT environments. Long-term support (15 years post-delivery) and intellectual property rights (IPR) transfer to ADA are non-negotiable.
Procurement and Commercial Framework
The bid, valued with an Earnest Money Deposit (EMD) of INR 4,42,000 and a 5% Performance Security, follows a two-packet (techno-commercial and price) evaluation on GeM. Key commercial terms include:
Payment Structure: 15% advance, 15% post-SATP, 20% after integrated ATP, and 50% upon final commissioning, all tied to milestones certified by ADA’s project coordinators.
Delivery: FOR ADA, Bangalore, within 365 days, including acceptance.
Warranty: Three years from acceptance, with free upgrades and immediate issue resolution.
The process adheres to India’s “Make in India” and MSE preference policies, prioritizing Class 1 local suppliers with at least 50% local content. A reverse auction eliminates the highest-priced bidder, ensuring cost-effectiveness.
Challenges and Innovations
Developing the SCTF poses challenges such as achieving high-precision signal handling, ensuring electromagnetic compatibility (EMC), and meeting stringent reliability standards. Innovations include the use of modular, rugged designs, built-in self-test features (POST), and a flexible BOB system for dynamic signal routing. The emphasis on proprietary development and complete IPR handover underscores ADA’s commitment to self-reliance in defense technology.
Conclusion
The SCTF for LCA AF Mk2 is a cornerstone of the aircraft’s development, bridging structural integrity with control system performance. Its successful implementation hinges on a meticulous blend of advanced engineering, rigorous testing, and robust vendor collaboration. As of March 24, 2025, this project exemplifies India’s strides toward cutting-edge aerospace capabilities, ensuring the LCA AF Mk2 meets global standards while bolstering national defense infrastructure.